About Us
Our companies' reputations are founded on superior product quality and unmatched customer service. In almost 100 years of business, we have never had an early failure complaint. We have been taught to always build on a solid foundation, and we view our product as the foundation that utilities build their businesses on. With that in mind, we are using the same proven processes to treat our Penta or DCOI utility poles. The most important part of the treating process is preparing/conditioning the wood prior to treatment. There are a few options for conditioning the wood including air seasoning, kiln drying, or steam conditioning; we specialize in the steam conditioning process because the properties of steam are “self-correcting” and ideal for conditioning wood. The properties of steam make it a self-correcting heating method because the steam heats the wood by condensing on the cooler surfaces of the pole which lowers the pressure and draws more steam to those cooler areas. As a result, the entire charge heats at a very consistent rate. It is a self-correcting and forgiving process in that it is not dependent on an operator loading the charge perfectly. The wood is treated properly and consistently from top to bottom, from small poles to large poles, from the outside edge of the charge to the middle, as well as from batch to batch.
Our goal in the steaming process is to heat the wood for an adequate amount of time to stop any incipient decay that may have started as well as to remove enough moisture from the wood during vacuum drying so that the preservative will penetrate all the way to the heartwood. Our goal is to manufacture a pole that will have a service life of 50+ years, not a pole that meets the minimum specifications. Additional benefits of our steam conditioning process include an easier to climb surface due to no case hardening effect from kiln drying, a consistently drier surface and “no bleed” attributes associated with steam conditioned wood, and less brittleness in the wood because of the slower reduction of moisture content in the wood. We believe that the treating process that we employ is the best in the industry in terms of proven quality, which results in a much lower cost to our customer over the life of our product.
WHITE POLE SUPPLY
​
Meredith Pole & Timber Company, Fitzgerald, GA was started in 1955 but rebuilt from the ground up in 1997. Meredith Pole & Timber represents the state-of-the-art in white pole mills with a capacity of approximately 600 to 800 poles/day. Meredith Pole & Timber is a woman owned business with the majority of the stock held by Amy Meredith Schneider – the fourth generation of the Meredith family carrying on the family tradition. We also purchase poles from several independent mills in Georgia, North Carolina, South Carolina, Florida, and Alabama to supplement our production capacity.
TREATING CAPACITY
​
For DCOI and Penta - William C. Meredith Company, East Point, GA.
Poles are framed, steam conditioned, and treated with Penta in East Point, Ga.. We currently operate with two steaming/treating cylinders that are 8' in diameter and 92' long. The plant was rebuilt and modernized in 2009 to include complete PLC/computer control of conditioning and treating process. WCM has all the necessary equipment and manpower to supply and support both treating cylinders on a continuous basis.
For CCA and CCA-ET - Partnered with CCA treating companies
Poles that are to be treated with CCA go through the same quality process including framing in East Point before being shipped to our CCA treating partners to be treated with CCA or CCA-ET. Our CCA treating partners perform their own quality control for the CCA treatment, but all poles recieve a second round of quality control when they arrive back to our distribution point in East Point, Ga..
INVENTORY AND TREATING TIME
​
AMS maintains an average 60-day inventory for all customers strategically located to provide prompt delivery schedules. These inventories consist
of all treated pole sizes and classes that are used by each of our regular customers.
White poles are trucked daily from the pole mills to our treating plant to cover any special needs and/or inventory shortages. Because we maintain a 60-day inventory of treated poles, we are able to make short notice treating schedule changes to cover a customer's emergency needs. Normal lead time from shipment to stock is about 1 to 2 weeks; normal lead time for special pole treatments is about 2 to 3 weeks after receipt of order.
DISTRIBUTION POINTS
​
East Point, GA – Inventory of Penta and CCA poles are distributed by truck using Barnes Transportation and by rail using Norfolk Southern. All truck delivers are made using self-unloading equipment.
​
St. James, MD – Inventory of Penta poles are received from East Point, GA via Norfolk Southern rail cars, unloaded and stored by Utility Supply, and delivered to the final destination by Barnes Transportation.
​
New England / New York – we partner with Stella/McFarland for supply and distribution of poles in the Northeast quadrant of the United States.
​
Blackshear, GA – CCA poles are distributed by truck using Barnes Transportation or ACE Pole trucks and by rail using CSX. All truck delivers are made using self-unloading equipment.
​
Fitzgerald, GA – Inventory of Penta poles are distributed by truck using Barnes transportation and by rail using CSX. All truck delivers are made using self-unloading equipment.
INVENTORY AND TREATING TIME
​
AMS maintains an average 60-day inventory for all customers strategically located to provide prompt delivery schedules. These inventories consist
of all treated pole sizes and classes that are used by each of our regular customers.
White poles are trucked daily from the pole mills to our treating plant to cover any special needs and/or inventory shortages. Because we maintain a 60-day inventory of treated poles, we are able to make short notice treating schedule changes to cover a customer's emergency needs. Normal lead time from shipment to stock is about 1 to 2 weeks; normal lead time for special pole treatments is about 2 to 3 weeks after receipt of order.

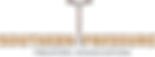

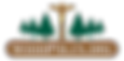
